
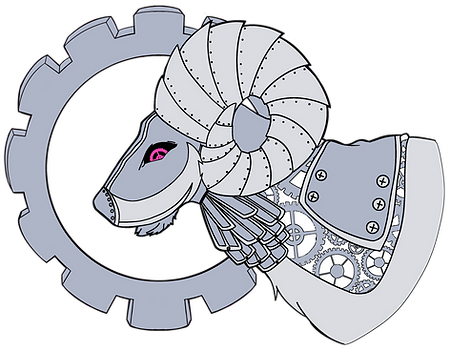

We Don't Just Build Bots | We Build Futures.

Meet Godzilla
All new year means all new challenge. In January 2025 Robotics First revealed REEFSCAPE. As our team was reviewing the new game field and scoring objectives for this competition we needed to determine our strategy. What would give our bot the necessary advantage? Everyone agreed that meant our robot should have a low center of gravity but with an arm reach capable of scoring on all levels of the coral reef. This meant our arm would need to reach to the highest level 4 on the game challenge. These two factors would give us the speed and stability needed to dominate the course while still allowing for the agility required to score big in competition. The beast we created to traverse the REEFSCAPE of 2025, had to be named after the fierce and amphibious Godzilla.
Thinking out of the box means making what you need from scratch. Like all of our robots, Godzilla features multiple custom CAD/CAM parts. We use Fusion 360 to design what we need and then the parts are manufactured on our two Haas Mini Mill CNC’s. Godzilla feaures 2 Degrees of Freedom - Double Jointed Rack & Pinion Arms, Control Box for pre-programmed movements referencing AprilTags and/or set field position as well as Camera Targeted Positioning for Loading and Scoring.
Meet K.I.S.S.
As our team was developing our initial design and gameplay concepts in 2024, the overwhelming consensus was our bot should be reliable. In industry, reliability goes hand in hand with simplicity. Combining the simplicity and scoring capabilities with a robot short enough to easily drive under the stage, led us to our overall theme and name of our bot: Keep It Super Simple. The geometric progressions in prototyping and CAD, gave us a simple but elegant solution for a rotating scoring arm with two degrees of freedom design that was capable of achieving our goals.
K.I.S.S features over 50 custom CAD/CAM parts. Fusion 360 is used by our team to design and the parts are then manufactured on our two Haas Mini Mill CNC’s. Our team chose to utilize SwerveDrive due to both the open field and the need to maneuver in the close confines of the alliance’s wing. Ball bearing roller pinions instead of chains or sprockets minimized backlash and increase speed and precision.


Meet Brass Monkey
In 2023 the ability to manipulate and score the different game pieces was a high priority in our design decision matrix. Our initial solution was a separate intake and hand off to a grabber for scoring, but after prototyping, our team quickly realized that a triple roller design on a three degrees of freedom arm would be more efficient. The Intake Wrist has a sprung joint to allow controlled recoil to prevent damage. A reliable docking on the charge station is integral to consistently winning and scoring ranking points and consistent hands-free self balancing was a requirement in our robot design.
In the past, we have had significant production schedule delays when relying on an outside machine shop to produce a part for us. To overcome this challenge, Brass Monkey features over 50 custom CAD/CAM parts. Fusion 360 is used by our team to design and the parts are then manufactured on our two Haas Mini Mill CNC’s.
Meet Giant Enemy Spider
Our 2022 robot was built with climbing in mind. This led us to the following: clamp and forget pivoting climb, 7 second high bar climb, utilize encoders to accelerate and decelerate winch speed based upon proximity to high bar, co-pilot engages direction with a custom joystick and lockout button - encoders determine velocity​ as well as Pneumatics control deployment of climb arms. An adjustable hood turret was also a high priority in our design decision matrix. After prototyping, our team quickly realized that cargo bouncing out was going to be a major problem. Our solution was to add a top roller to the adjustable hood to reduce/eliminate the backspin which was causing the cargo to bounce out.
Our team chose to utilize a West Coast Drive due to familiarity and reliability. We did migrate to a chain-in-tube system to minimize adverse leverage on the drive wheels and gearboxes. This C-I-T system also protects and minimizes problems with the chain. Giant Enemy Spider features over 150 custom CAD/CAM parts.
​
